The design of tanker trailers is a complex process that involves a multitude of factors to ensure the safe and efficient transportation of various liquids and gases. Here is an overview of the critical elements that must be considered in the design of tanker trailers .
1. Materials and Construction
The choice of materials is paramount in tanker trailer design. Tanks are typically constructed from high-strength steel, aluminum, or stainless steel, depending on the type of liquid being transported . The thickness of the tank walls is crucial for maintaining structural integrity, especially when transporting hazardous liquids like natural gas liquids (NGL) and chemicals . Thicker walls are necessary to prevent leaks or ruptures in the event of an accident and to withstand the pressure required for hauling these products .
2. Tank Geometry and Structural Integrity
The geometry of the tank plays a significant role in ensuring safe liquid transfer. Tanks are designed to withstand the stresses and strains of transportation, including the weight of the liquid and road vibrations . Cylindrical or elliptical shapes with a low center of gravity help prevent rollovers . Baffles or partitions can be included to prevent liquid sloshing during transportation .
3. Safety Features and Standards
Adherence to safety standards is non-negotiable. Tanker trailers must be equipped with an array of safety features, including pressure relief valves, emergency shutoff valves, and spill containment systems . Regular inspections ensure these features remain in optimal working condition, providing an additional layer of safety and reliability .
4. Chemical Compatibility
Chemical compatibility is crucial for safe chemical transfer. Materials used in tank construction, seals, hoses, and other components must be compatible with a wide range of chemicals . Extensive testing is conducted to ensure tanks are resistant to corrosion and chemical degradation .
5. Pressure and Design Specifications
Different types of tanker trailers have specific design pressures. For instance, DOT 407 crude oil tank trailers operate at 25 PSI, while DOT 412 corrosive material tankers handle higher pressures above the 35-50 psig range . MC-331 high-pressure cargo tankers, designed for compressed gases, often exceed 250 psi .
6. Loading/Unloading Facilities
Efficient loading and unloading are essential. Tankers are equipped with bottom loading facilities for safe and efficient material transfer . Some tankers also feature top loading facilities .
7. Compartments and Insulation
Tankers can be built in single or multiple compartments, depending on the needs . Insulation is a consideration for tankers operating in colder climates to maintain the integrity of the cargo .
8. Emergency Features
Emergency features such as venting facilities, vapor recovery systems, internal valves, overfill protection, and rollover rail protection are critical for the safe transport of hazardous materials .
The design of tanker trailers is a sophisticated process that requires careful consideration of materials, construction, safety features, chemical compatibility, and compliance with pressure and design specifications. By adhering to these principles, the transportation industry can ensure the safe and efficient transfer of liquids and gases, protecting both the environment and public safety.
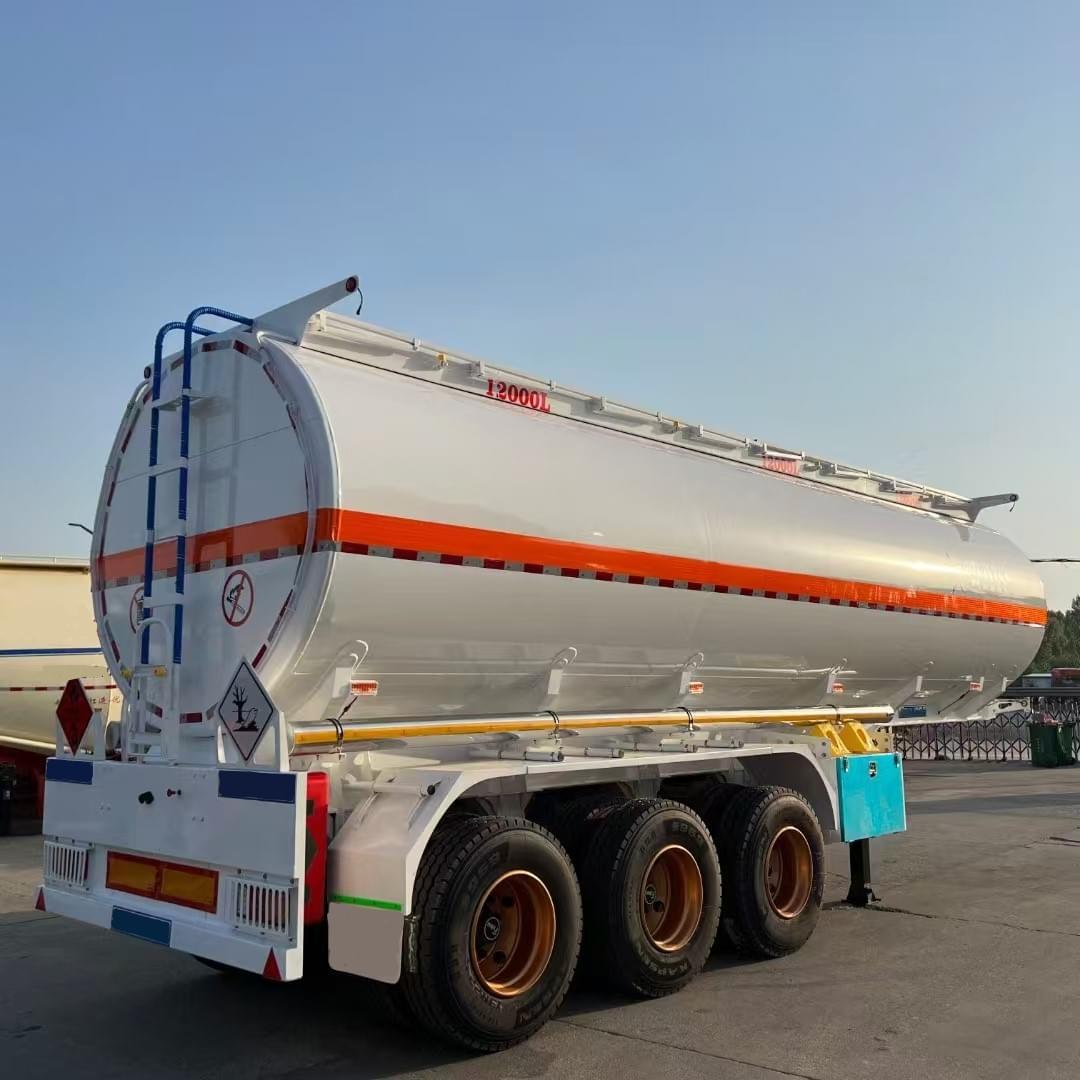