Refrigerated trailers, also known as reefer trailers, are an essential component of the cold chain logistics industry. They are designed to transport perishable goods, such as food and pharmaceuticals, over long distances while maintaining a controlled temperature. This article will explore the key design considerations that go into creating an efficient and reliable refrigerated trailer.
1. Thermal Efficiency:
The primary function of a refrigerated trailer is to maintain a stable temperature. Therefore, thermal efficiency is a critical design consideration. Insulation plays a vital role in this aspect. The walls, floor, and ceiling of the trailer should be constructed with high-quality insulation materials to minimize heat transfer. This ensures that the cargo remains at the desired temperature, reducing the need for frequent temperature adjustments and energy consumption.
2. Refrigeration Units:
The refrigeration unit is the heart of the refrigerated trailer. It must be capable of maintaining the required temperature range and have the capacity to cool the trailer quickly after loading. Modern reefer trailers often use diesel-driven refrigeration units, which are more reliable and efficient than electric units. The design should also consider the placement of the unit to ensure optimal airflow and cooling efficiency.
3. Airflow Management:
Proper airflow management is essential for maintaining uniform temperature throughout the trailer. The design should include features such as air ducts and vents that direct the cold air evenly across the cargo space. This prevents hot spots and ensures that all items within the trailer are kept at the correct temperature.
4. Load Securing:
The design of the trailer must also accommodate the securement of the cargo. This includes the use of anchor points, straps, and other securing devices to prevent the cargo from shifting during transit. This is particularly important for heavy or bulky items that could damage the trailer's insulation if they come into contact with the walls.
5. Structural Integrity:
Refrigerated trailers are subject to harsh conditions, including temperature fluctuations, humidity, and physical stress from loading and unloading. Therefore, the trailer's structure must be robust and durable. Materials such as aluminum and stainless steel are often used for their strength and resistance to corrosion.
6. Temperature Monitoring and Control:
Modern refrigerated trailers are equipped with sophisticated temperature monitoring systems that allow for real-time tracking of the cargo's temperature. This data can be transmitted remotely, allowing for immediate action if the temperature deviates from the set point. The control system should be user-friendly and capable of adjusting to different temperature requirements for various types of cargo.
7. Energy Efficiency:
With increasing environmental concerns, the design of refrigerated trailers must consider energy efficiency. This can be achieved through the use of energy-efficient refrigeration units, LED lighting, and aerodynamic design features that reduce fuel consumption during transport.
8. Compliance and Regulations:
The design must comply with various national and international regulations regarding the transportation of perishable goods. This includes standards for temperature control, cargo securement, and the safe operation of the trailer.
The design of a refrigerated trailer is a complex process that involves balancing thermal efficiency, structural integrity, and technological advancements. By considering these factors, manufacturers can create trailers that are not only reliable and efficient but also compliant with the latest industry standards. As the demand for temperature-controlled transportation continues to grow, the importance of innovative design in refrigerated trailers cannot be understated.
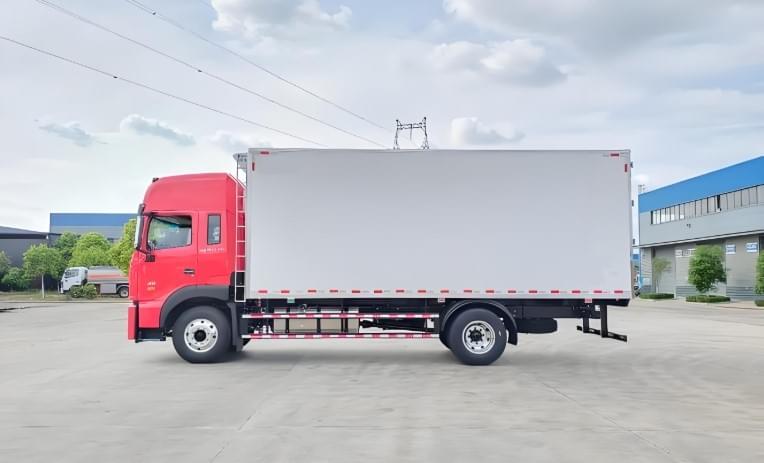